Unlock a World of Printing Possibilities With UV DTF Printing
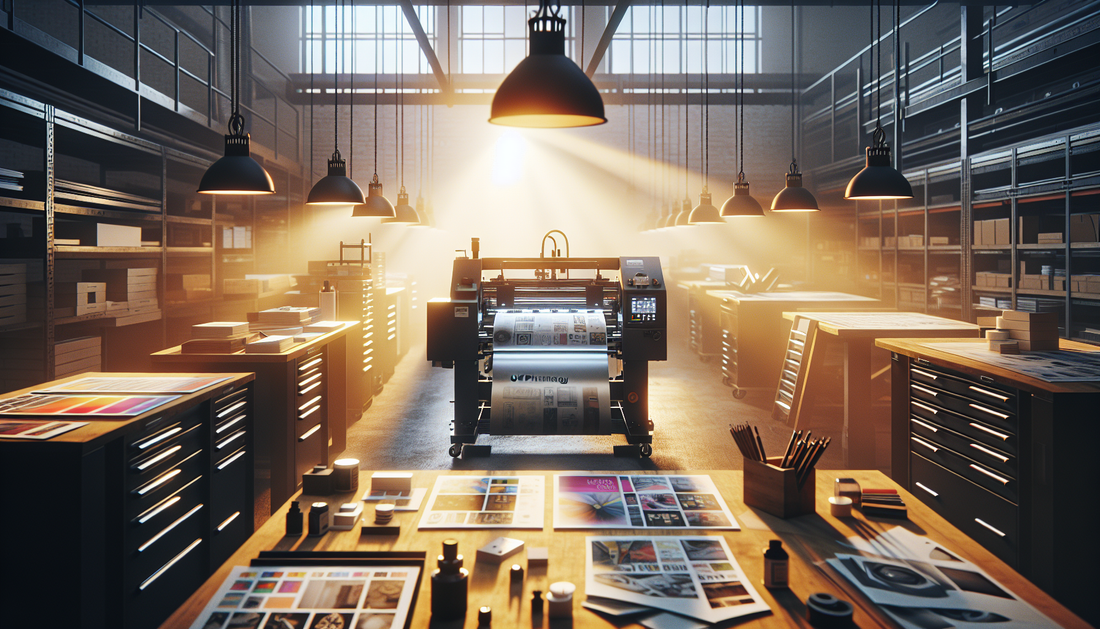
Introduction to UV DTF Transfer
Ultraviolet (UV) direct-to-film (DTF) transfer is an innovative printing technology that is gaining popularity for its ability to produce high-quality and durable prints on a wide variety of materials. It combines the advantages of UV curable printing and heat transfer to enable stunning image transfer onto everything from phone cases and t-shirts to wood, metal, acrylic, leather, and more.
This versatile printing process provides new possibilities for customization and personalization in the promotional products, apparel decoration, packaging prototyping, labels and stickers, and 3D printing industries. As the technology develops further, UV DTF looks set to become an accessible and eco-friendly solution for creative applications.
What is UV DTF Transfer?
UV DTF transfer allows you to print designs straight onto a special transfer film using ultraviolet (UV) curable inks. This printed film is then transferred onto the final substrate using heat and pressure. The UV inks instantly cure and bond to the film with UV light, allowing it to be quickly handled or further processed.
The basic process involves:
- Printing the design onto the UV DTF transfer film using a UV printer
- Applying a thermal laminate over the printed design
- Cutting out the printed design from the film
- Heat pressing the film onto the final substrate
- Peeling away the transfer film, leaving the printed design permanently bonded to the surface.
So UV DTF transfer effectively bridges the gap between digital printing and heat transfer. It harnesses the high print quality and customization potential of UV inks as well as the versatility and durability of heat transfer.
What are UV-Curable Inks?
The technology behind UV DTF transfer lies in the use of UV-curable inks. These are specialty inks that cure and set instantly when exposed to ultraviolet light. This enables much faster printing and processing compared to other ink technologies.
UV inks contain photoinitiators - special molecules that cause polymerization when exposed to the right UV wavelength. This transforms the inks from liquid to solid, bonding them to the print surface.
Key benefits of UV-curable inks include:
Extremely Fast Drying
As the inks cure instantly under UV light, drying times are eliminated. This allows for faster print production.
Excellent Adhesion
The instant curing reaction creates superior adhesion between ink and surface for added durability.
High Resolution
Precise dot control allows for sharp image reproduction, fine details and high print resolution.
Increased Durability
Being impervious to moisture, UV prints better withstand wear and tear, abrasion, and exposure without fading or peeling.
No Solvents or VOCs
UV inks contain no volatile organic compounds (VOCs) or hazardous air pollutants (HAPs) making them safer and eco-friendly.
These properties perfectly suit UV DTF transfer where high print quality needs to reliably transfer onto various materials.
Advantages and Disadvantages of UV DTF Transfer
UV DTF transfer brings some unique benefits but also has a few limitations to consider.
Advantages of UV DTF
Works on a Wide Variety of Materials
From fabrics like cotton, polyester, spandex blends to leather, wood, acrylic, glass, and metal, UV DTF can print on an immense range of materials that traditional screen printing cannot.
Superb Print Quality and Vibrancy
Using UV inks allows for stunningly vibrant and crisp prints that really make designs pop on the substrate.
Highly Durable Prints
The flexible and stretchable prints bond strongly and resist fading, chipping or peeling, even under frequent use and washing.
Cost-Effective Short Runs
Minimal setup costs mean UV DTF is ideal for sample prototyping or small custom print batches.
Eco-Friendly Process
With no VOCs and lower energy consumption, UV DTF has less environmental impact than traditional printing.
Disadvantages of UV DTF
High Initial UV Printer Investment
Specialty UV-DTF printers can involve considerable upfront costs of $10,000 upwards.
Limited Size Capabilities
Although improving, maximum print sizes top out at around 14 x 16 inches for most desktop UV-DTF printers.
Special Substrates May Be Required
To achieve the high transfer success rate, coated transfer films designed for UV-DTF may need to be used.
Slower Than Screen Printing for High Volumes
Above a few hundred prints, screen printing becomes the cheaper and faster mass production method.
So UV DTF offers a highly customizable and eco-friendly solution for short runs, sample prototyping, and specialty printing applications. It enables stunning prints on an ever-growing range of materials.
UV Direct to Film Printing Process
The UV DTF transfer process generally involves six key steps:
1. Prepare and Edit Design
- Create or edit design in editing software
- Set up color separations if needed
- Ensure suitable resolution and size
2. Print Onto UV DTF Transfer Film
- Load transfer film into UV-DTF printer
- Select substrate material
- Print design onto transfer film
3. Laminate Printed Film with Transfer Film
- Apply thermal laminate to printed transfer film
- This protects ink and assists heat transfer
4. Cut Out Image
- Use plotter/cutter to contour cut printed design
- Weed away excess transfer film
5. Heat Press Film Onto Substrate
- Heat press transfer film onto substrate as per instructions
- Pressure and heat needed vary per material
6. Peel Back Transfer Film
- Allow to cool then gently peel back transfer film
- Printed design remains securely bonded to material
Getting the right combinations of temperature, pressure and time is vital for successful material transfer. Most UV DTF printers come with parameter guides for common materials.
UV DTF Film Types
There are two main types of specialist films used in the UV DTF transfer process:
1. Print Film
The print film is the material that the UV-curable ink is directly printed onto. It has a matte or gloss finish and is coated with a heat-activated adhesive. Common materials used include polyurethane, polyester, and vinyl.
2. Transfer Film
After printing, a hot or cold peel transfer film is applied on top of the print film using a thermal laminator. This protective layer supports the print film during handling and transfer. It gets peeled away after heat pressing the design onto the final substrate.
Using the combination of these specially engineered films allows for hassle-free printing, cutting, weeding and transferring of designs even for complete beginners.
Pricing and Cost Considerations in UV DTF Printing
As with any printing technology, there are several factors that determine overall costs for UV DTF transfer:
Printer Investment
- Desktop UV-DTF printers roughly range from $10,000 to $50,000. Additional costs for laminator, cutter.
- Production capacity, print size, ink capability affect pricing.
Ink and Film Costs
- Specialty UV-DTF inks average $200 per liter. Films $30+ per 15 yard roll.
- Ink and film usage calculated per square foot printed.
Labor Time
- Artist/operator design, print, finishing time impacts labor costs.
- Automated workflows improve efficiency.
Setup Fees
- Prepping films, inks, printer settings takes time initially.
- Typically waived for reorders.
Quantity of Prints
- Unit pricing drops significantly with order volumes above 100-500 prints.
- Digital nature means low volumes are still cost effective.
Profit Margins
- Markups average 30-50% retail over production costs.
- High perceived value of customization enables healthy margins.
The digital nature of UV DTF makes it cost effective for sample prototyping and small custom print runs of up to 500 units. At higher production volumes, outsourced screen printing becomes more affordable.
However the ability to efficiently print short runs with fast turnarounds makes UV DTF highly profitable for print providers. Its environmental benefits also allow businesses to tap into the growing market for sustainable printing solutions.
Conclusion
In conclusion, UV direct-to-film transfer offers immense possibilities for innovative printing applications. This game-changing technology bridges digital UV printing and heat transfer to enable stunning, durable image transfer onto an exceptional range of materials.
UV DTFβs use of instant-curing UV inks facilitates superior print quality and faster turnarounds. It expands the design potential for customizing and personalizing products, packaging, apparel and more. While requiring some initial investment, UV DTF provides an eco-friendly, cost-effective solution for creative short runs and on-demand production needs.
As the selection of compatible substrates and production capacities grow, UV DTF transfer looks set to transform digital printing. Its ability to print-on-demand directly onto final surfaces reduces inventory while opening up new levels of mass customization. With capabilities improving all the time, UV DTF presents an exciting future of digitally printed products that can be as unique as the individuals who use them.