Unlock the Secrets: How to Achieve That Dreamy Softer DTF Transfer!
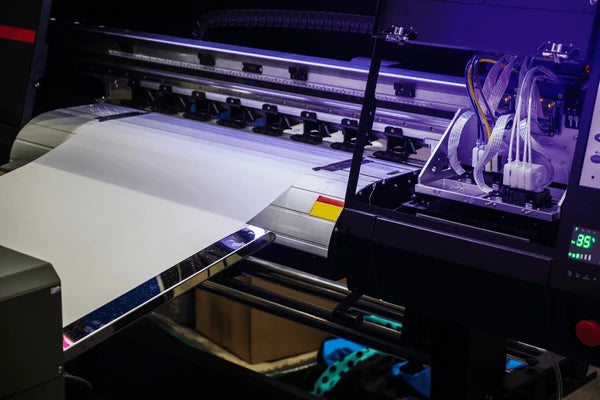
Unlock the Secrets: How to Achieve That Dreamy Softer DTF Transfer!
Are you looking to take your DTF t-shirt printing game to the next level? One key aspect is achieving that soft, comfortable feel that customers love. Hard, plasticky prints can be a real turnoff. But don't worry - with a few simple techniques, you can create DTF transfers that are super soft and dreamy to the touch.
Key Takeaway | Explanation |
---|---|
Use a black knockout halftone effect | Removing the black background and replacing it with a halftone preserves details while making the print lighter, more breathable and softer. |
Choose the right DTF transfer film | Thin, flexible films designed for soft hand feel will produce a softer print compared to thick, rigid films. Transparent films also tend to feel softer than opaque white. |
Adjust printer settings to reduce ink | Using just enough ink to get a vibrant print without over-saturating will help avoid a thick, plasticky feel. Experiment with slightly lower ink density settings. |
Print on soft, lightweight fabrics | Natural fibers like cotton and thin, lightweight fabrics will conform better to the print, making it feel softer compared to thick, heavy synthetic fabrics. |
Pre-press garment before applying transfer | Pressing the shirt first creates a smooth, even surface that allows the ink to absorb more evenly into the fibers for a softer feel. |
Use medium pressure and temp when pressing | Around 300Β°F and medium-firm pressure for about 15 seconds is optimal. Avoid excessive pressure and heat which can make the print stiffer. |
Consider a distressed or halftone design | Distressed, faded or halftone printed designs tend to naturally feel much softer compared to heavy solid blocks of color ink. The thinner ink layer creates a vintage softness. |
Understanding Textures of DTF: Why DTF Prints Can Feel Hard
First, it's important to understand what causes DTF prints to sometimes feel stiff or plasticky:
- The quality and thickness of the transfer film used
- Pressure and heat settings during the transfer process
- The type of fabric being printed on
- The specific ink or toner used
Getting the combination of these factors right is key to a soft hand feel. Let's dive into some tips to optimize each one.
Choosing the Right DTF Transfer Film
The PET film you use for DTF printing makes a big difference in the final feel. Look for transfer films that are:
- Thin and flexible
- Specifically designed for soft hand feel
- Lighter in color (transparent films tend to feel softer than opaque white)
Using a high quality soft touch transfer film as your base will go a long way in creating a comfortable print.[3]
Adjusting Your Printer Settings
The amount of ink or toner laid down also impacts the texture. To avoid a thick, plasticky feel:
- Reduce the overall ink density in your printer settings
- Use just enough ink/toner to achieve a vibrant print, but not more
- Consider a slightly textured or matte finish rather than glossy
Experimenting with your printer settings allows you to dial in the optimal ink levels for a softer result.[8]
Choosing the Right Fabric for Softer DTF Feel
The garment itself also plays a role in the final feel. Natural fibers like cotton, bamboo, and modal blends tend to have a softer texture compared to synthetics like polyester.
Whenever possible, opt for thinner, lightweight fabrics. The print will conform and meld better with finer materials vs thick, heavy garments. Tri-blends and 100% ringspun cotton are great choices.[3]
The Importance of Pre-Pressing on Garment
Don't skip the pre-press step! Pressing your garment before applying the transfer film helps create a smooth, even surface. This allows the ink to absorb more evenly into the fibers.
Pre-pressing also removes wrinkles, moisture and texture irregularities in the fabric that could make the print feel rougher.[18]
Perfecting Your Heat Press Technique
Proper heat press settings are critical for a soft touch DTF print:
- Use medium-firm pressure (not too heavy)
- Keep temperatures around 300Β°F
- Press for about 15 seconds
Peel the transfer film according to the manufacturer's instructions, usually cold. Experiment with doing a quick re-press with a sheet of parchment paper to further set and soften the ink.
Bonus Tip: Try a Distressed or Halftone Design
Finally, consider the design itself. Distressed, faded, or halftone effects tend to feel much softer than heavy, solid blocks of color.[1] The thinner, broken-up layer of ink creates a vintage softness.
You can achieve a halftone look in Photoshop by converting your design to grayscale, then bitmap. Adjust the frequency and angle of the halftone dots to get the perfect faded effect.[1]
With these tips and tricks, you'll be creating buttery-soft, high-end feeling DTF prints that your customers won't be able to keep their hands off of! It's all about choosing the right materials, dialing in your settings, and getting creative with your design. Happy soft touch printing!
FAQs - Learn more about DTF Texture
What does a DTF transfer feel like on a shirt?
Direct to Film (DTF) transfers on a shirt typically result in a soft and smooth feel on the fabric, offering a comfortable wearing experience. Unlike some other printing methods, DTF transfers feel lighter and more flexible, seamlessly integrating with the fabric's surface. The texture can range from barely perceptible to slightly raised, depending on factors like ink thickness and finishing techniques. Overall, a properly executed DTF transfer enhances both the visual appeal and comfort of the garment, providing a high-quality finish that feels pleasant against the skin.
What are the disadvantages of DTF?
While Direct to Film (DTF) printing offers several advantages, such as the ability to print vibrant and detailed designs on various fabrics, there are also some notable disadvantages to consider. Firstly, DTF printing requires specialized equipment and consumables, which can be expensive to acquire and maintain compared to other printing methods. Additionally, the process can be time-consuming, especially for intricate designs, as it involves multiple steps including printing, curing, and transferring the film onto the fabric. DTF transfers may also have limitations in terms of wash durability and longevity compared to other printing techniques like screen printing or heat transfer vinyl. Moreover, achieving consistent color accuracy and quality control can be challenging with DTF printing, particularly when dealing with complex designs or large batches of prints. Finally, environmental concerns may arise due to the use of chemicals and waste generated during the printing process, highlighting the importance of proper disposal and sustainability practices.
What is the best heat press setting for DTF?
For optimal DTF (Direct to Film) printing results, several key heat press settings need consideration. Generally, temperatures between 320Β°F to 340Β°F (160Β°C to 170Β°C) are recommended, although specific film requirements should be consulted. Moderate to firm pressure ensures proper adhesion of the film onto the fabric, with pressing times typically ranging from 20 to 30 seconds. After the pressing cycle, allowing the fabric to cool briefly before peeling off the carrier sheet ensures a smooth and effortless peel, indicating successful adhesion. It's essential to conduct testing to fine-tune settings for color vibrancy, adhesion, and wash durability, while always adhering to manufacturer guidelines for optimal DTF printing outcomes.
What is the best DPI for DTF?
The best DPI (dots per inch) for DTF (Direct to Film) printing depends on various factors such as the resolution of the printer, the intricacy of the design, and the desired quality of the final print. However, a DPI of around 300 or more is commonly recommended for DTF printing to achieve high-quality results with sharp details and vibrant colors. Some advanced printers may even support higher DPI settings for more intricate designs or larger print sizes. It's essential to balance DPI with other factors such as printing speed and ink consumption to optimize printing efficiency and output quality. Conducting test prints at different DPI settings can help determine the optimal resolution for your specific printing setup and requirements. Additionally, always refer to the printer manufacturer's recommendations and guidelines for the best DPI settings for DTF printing.
Tips for Making DTF Prints Feel Better! How to Soften DTF!
1. Choose high-quality DTF films designed for optimal printability and adhesion.
2. Adjust printer settings such as resolution, ink density, heat, and pressure for desired texture.
3. Experiment with different ink types, finishes, and post-processing techniques to enhance tactile feel.
4. Implement rigorous quality control measures to ensure consistency and excellence in print texture.
Conclusion
In conclusion, achieving a soft, comfortable feel on DTF t-shirt prints requires careful consideration of several key factors throughout the printing process. By selecting the right DTF transfer film, optimizing printer settings, choosing soft and lightweight fabrics, properly pre-pressing the garment, using appropriate heat press techniques, and incorporating distressed or halftone design elements, you can create DTF prints that are incredibly soft to the touch and a pleasure to wear.
Experimenting with different combinations of these variables allows you to fine-tune and perfect your method for consistently producing soft, high-quality prints. The black knockout halftone effect is an especially effective technique for preserving design details while making the print lighter, more breathable, and softer overall.
With a bit of practice and attention to detail in each step, you'll be well on your way to mastering the art of soft hand DTF printing. Your customers will be thrilled with the premium look and feel of their custom t-shirts. So go ahead and put these tips into action - your softest, most comfortable DTF prints await!